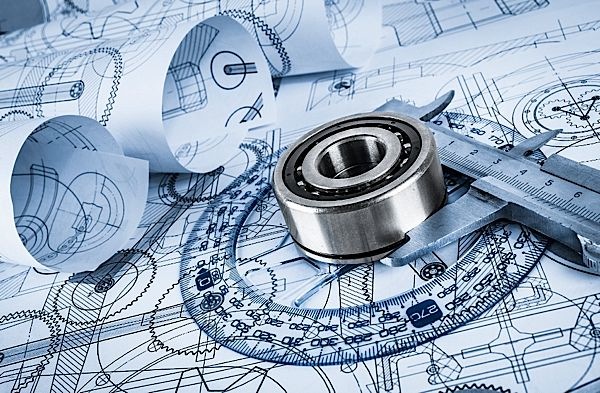
Pandemic-proofing projects and operational sites with remote engineering support
Posted on 17th Jul 2020
Article Waterline
Since 2019, 75 per cent of Waterline’s multi-disciplinary engineering projects were delivered without an engineer ever setting foot onsite.
Initially unintentional, this remote model became a key function of this engineering consultancy’s approach throughout the COVID-19 pandemic, as accessing the site was no longer an option across the Queensland resources industry, where 85 per cent of its work was based.
Due to travel and personnel restrictions imposed by the pandemic, resourcing impacts posed a very real risk to the productivity, safety and compliance of the operations of Waterline’s mining clients.
Remaining essential
Waterline has remained essential to these essential services by safeguarding the fundamental engineering roles traditionally carried out onsite. These are the day-to-day essentials that could be taken offsite and delivered fully remotely, guaranteeing continued support. Waterline’s Operations Manager, Steven Cheyne, says that becoming a pseudo-site team was critical to removing risk.
“Because our team have operational backgrounds, we understood the challenges, risks and cadence of sites,” he says. “Additionally, upscaling our workforce by 25 per cent, moving our engineering team fully remote, and reinforcing our remote engineering products, we were able to throw a safety net around our clients in Queensland mining. This meant that they no longer had a single failure point for those critical onsite roles regardless of the uncertainty, risks and restrictions imposed by COVID-19.”
According to Cheyne, the global pandemic has been a catalyst for many mining operations to review how they manage engineering activities onsite.
“We’ve seen an increase in demand for our remote products, such as 24/7 multi-discipline engineering and PCS support, 3D printed models of site equipment to improve communication to production crews, digitising paper-based processes allowing teams to work from anywhere, and drafting with a guaranteed 24-hour turnaround,” he says.
24-hour turnaround
Operations such as Anglo American’s Moranbah North Mine have transitioned their onsite drafting to Waterline’s Premium 24-Hour Turnaround Drafting Package.
Home to one of the largest coal reserves in the world, the site must maintain the accuracy of its engineering drawings at all times to ensure the continued safety of its personnel, as well as compliance with Queensland’s mining regulations.
Waterline manages the site document management system and critical drawing updates, fully complying with its 24-hour turnaround guarantee. This ensures that accurate drawings are available to its teams in real-time, whether onsite or remote.
Since engaging Waterline’s remote services, Moranbah North Mine’s Engineering Manager, Brendan Kelly, says that he has seen significant benefits across the mine’s engineering department and its trades in the field.
“We are now confident that we have reliable updates of our critical drawings, easily accessible by all our teams,” he says.
“This means the safety and efficiency of our tradespeople and engineers is improved. We also appreciate that Waterline’s drafters understand mining operations and we don’t have to spend the time giving them detailed instructions. Overall, this service is now essential to our operation.”