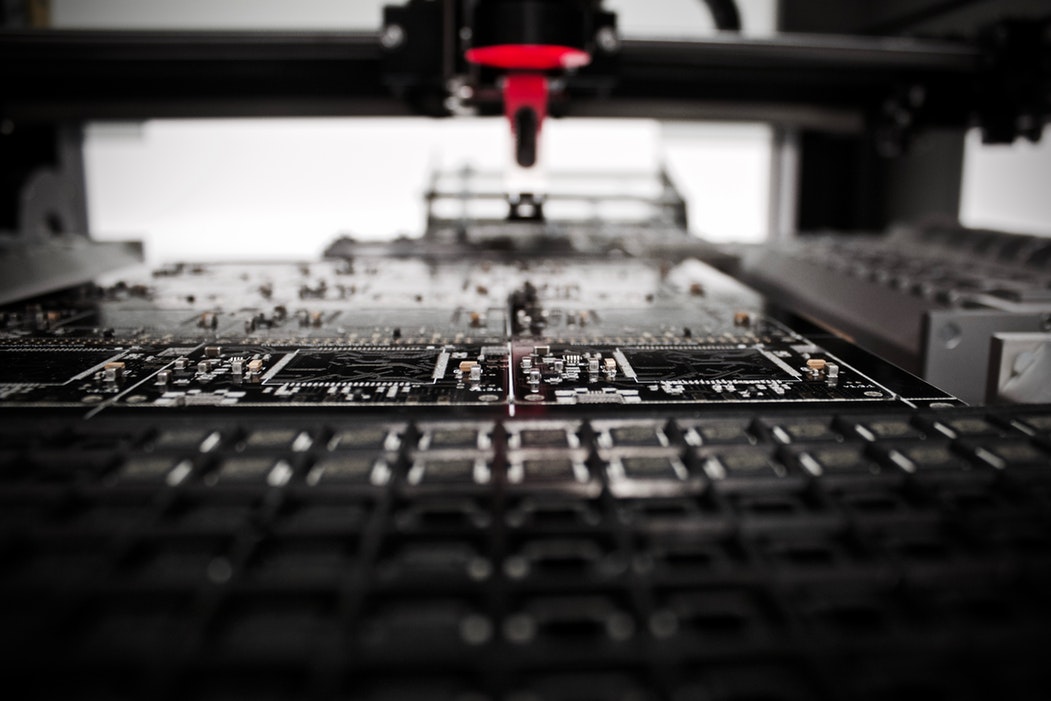
The Advantages of Using MRP Software in Manufacturing
Posted on 30th Oct 2018
Article By: mrpeasy
MRP Software – is a general term for automated software systems used for manufacturing resource planning. The main goal of MRP software systems is to make the process of production and material planning as easy and automated as possible, freeing up the human resources to perform more complicated tasks. MRP systems help to ensure that there is enough material for production, the right amount and at the right time. It also helps keep track of products available for delivery and helps to maintain the lowest possible material and product levels at the manufacturing facility.
The development of the information technology and the increase of the number of automated processes in modern manufacturing has made it possible not only to perform necessary calculations of material and production planning but also automate these processes. The more advanced MPR software nowadays can even make the changes to the amount of the material purchased automatically, automatically calculating the demand.
According to research conducted by our firm, about 50% of small manufacturers use manual methods, like Excel spreadsheets or even paper and pencil, for material requirements planning. Below is the list of what companies lose out on by not using the automated MRP software solutions:
Speed – the planning of materials and components needed for manufacturing is made much faster than using a simple Excel spreadsheet, for example. While Excel is OK for a one-man shop where a person is responsible for all parts of the business, from material purchase to product distribution, it is not a very versatile tool for bigger companies. Getting information from the sales department to the manufacturing and then purchasing takes time and human resources.
Using specialized MRP software would eliminate the problem of time being wasted on communication between the departments and sending the spreadsheets back and forth. By using one interface of the software, people from different departments can access the system simultaneously, make necessary changes and make them more accurately.
Safety – For companies having different product categories, suppliers and clients, using something like Excel being sent from person to person is not a good option. Files can get lost or simply deleted by mistake from the network.
The modern MRP software solutions use a safe and web based cloud technologies for information to be easily accessible online via any type of gadget, be it a laptop, a tablet or a mobile phone. A sales agent can enter the sales contract details in the system, while being with the client, sending the signal to the purchasing and manufacturing instantly. This communication is done via a safe and easy-to-use web application.
Accuracy – having multiple parties involved in the supply chain makes it challenging to keep all the information about components’ pricing, quantities and suppliers’ names accurate and up to date. It could be possible if the company has only a handful of suppliers. However, as the business gets bigger keeping track of all individual suppliers, let alone their shipments and components, is impossible. The same is true for the clients as well.
Using MRP software would easily eliminate the problem of making individual comments about current sale and purchase orders. Modern MRP software includes capacity planning, inventory control and warehouse management functionalities, providing the latest and most accurate up-to-date information about the current level of finished products, as well as planned material purchases.
Overall, a modern MRP software provides a real advantage to the manufacturer and affordable cost. Today there are plenty of different products available on the market for both medium and small companies. Some would argue that the biggest ERP system providers have the MRP already included into their systems, so there is no need for a separate software to be used on a factory floor.
The main problem here is that only the largest companies could afford to install a fully customizable and multifunctional ERP system from the top providers. The cost of integrating these systems with the current working conditions could take hundreds of thousands of dollars and several months of work. Running and using this software would also require having a team of specialists on staff who will be managing these complex solutions internally.
For a medium or a small manufacturing company there is no need to use big and complex solutions. While they would lose out on some features, the extra work and money it would need is not worth it. The better option is to use a more simple MRP software, tailored specially for the needs of small and medium size manufacturers.
This type of software has everything that a manufacturer needs to have a total control over the logistics and manufacturing part of material flow. In addition, solutions tailored for smaller manufacturers cost considerably less, have limited start-up costs, and are very easy to install and run from day one.