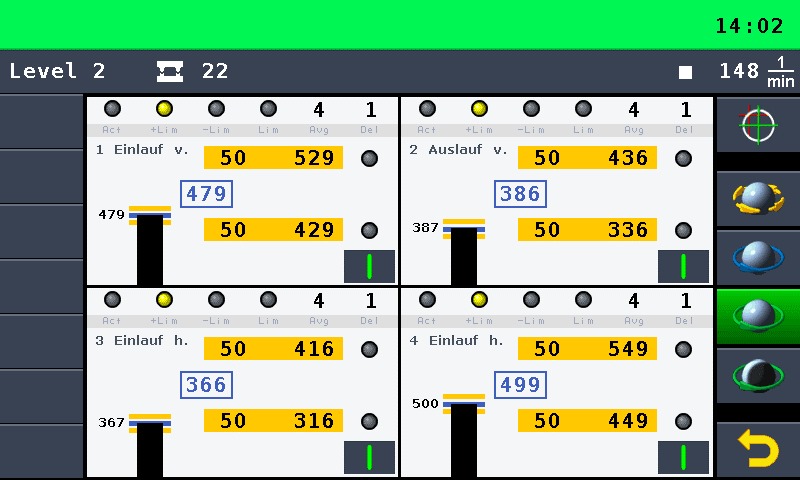
Press Monitoring with Automated Plunging Depth Capability
Posted on 10th Nov 2020
Marposs recently demonstrated its Brankamp X3S monitoring, control and measurement unit with a new plunging depth feature for high-speed stamping presses. This capability automatically compensates for machine process parameters-such as sheet thickness, material hardness, tool and machine temperature-that change during the stamping process via a connection with the press PLC.
"Although advanced presses can automatically correct the ram position during the manufacturing process and adapt it to changed production speeds, employing the Brankamp monitoring system enables a more extensive plunging depth control system," said a company spokesperson. This approach can detect and evaluate stop block forces during the stamping process using special control algorithms to carry out a step-by-step adjustment (step size 2 µm or 10 µm) of the ram position.
The stamping process and its clamping forces at the machine's lower reversal point are kept constant. At the same time, the machine operators are informed on-the-fly about plunging depth setting when the tools are set up, and the insertion height can be automatically adjusted to the optimum range. Depending on the complexity of the tool and the number of equipped stop blocks, a different number of limit stop forces can be included in the control system.
The X3S control system visualizes the calibrated force progressions and displays the control variables executed for the user. A standardized interface to the PLC makes it easy to connect the Brankamp control system to automatic stamping machines.
Effects on Product Quality and Tool Wear
According to the company, the use of the new insertion depth control systems offers numerous advantages for stamping companies:
Accelerates set-up time during tool change
Increases reproducibility of tool settings
Avoids excessive tool load due to excessive stop forces
Achieves consistent product quality, especially in bending and coining operations
Reduces swinging wear of piercing or blanking punches since no unnecessary ram oscillations in the lower reversal point of the machine are caused by premature contact with the stop blocks
Automates machine adjustment (without operator intervention) to varying material properties, especially after coil changing or over the coil length
Reduces scrap production
Increases productivity due to uninterrupted production
Reduces energy consumption.